Home Failure Analysis TIG Welding MIG Welding Flux Cored Welding Stick Welding SAW Resistance Welding Electron Beam Welding Robotic Welding Brazing & Soldering Expert Witness Experience Fees Links
Distortion
Discontinuities
Alloy Selection
Steel
Stainless
Steel
Aluminum
Section
IX of the ASME BPVC
ASME
P-Numbers
Structural
Welding
| |
MIG Welding
Gas Metal Arc Welding (GMAW) is frequently referred to as MIG welding.
MIG welding
is a commonly used high deposition rate welding process. Wire is continuously
fed from a spool. MIG welding is therefore referred to as a
semiautomatic welding process.
|
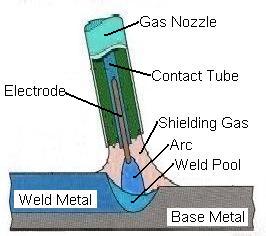
|
MIG Welding Benefits
- All position capability
- Higher deposition rates than SMAW
- Less operator skill required
- Long welds can be made without starts and
stops
- Minimal post weld cleaning is required
MIG Welding Shielding Gas
The shielding gas, forms the arc plasma, stabilizes the
arc on the metal being welded, shields the arc and molten weld pool, and allows
smooth transfer of metal from the weld wire to the molten weld pool. There
are three primary metal transfer modes:
The primary shielding gasses used are:
- Argon
- Argon - 1 to 5% Oxygen
- Argon - 3 to 25% CO2
- Argon/Helium
CO2 is also used in its pure form in some
MIG welding processes. However, in some applications the presence of CO2
in the shielding gas may adversely affect the mechanical properties of the
weld.
|
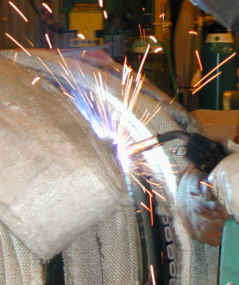
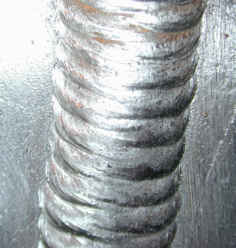 |
Common MIG Welding Concerns
We can help optimize your MIG welding process variables. Evaluate your current
welding parameters and techniques. Help eliminate common welding problems
and discontinuities such as those listed below:
- Undercutting
- Excessive melt-through
- Incomplete fusion
- Incomplete joint penetration
- Porosity
- Weld metal cracks
- Heat affected zone cracks
|
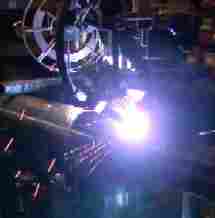
|
MIG Welding Problems
- Heavily oxidized weld deposit
- Irregular wire feed
- Burnback
- Porosity
- Unstable arc
- Difficult arc starting
If your company is experiencing these or other welding problems you can retain
us to improve
your weld processing. Hire us to act as your welding
specialist.
Contact Information
- Telephone
-
407-880-4945 -------- (Consulting is only available for customers)
- FAX
-
- Postal address
-
- Electronic mail
- General Information:
bob@WeldingEngineer.com
Customer Support:
bob@WeldingEngineer.com
Webmaster:
|